Have I ever lost tools on the job?! Let’s just say it’s a good thing I don’t need a pen to write this blog post or it would have never been finished. If you’re like me, you’re no stranger to the lost pen, screwdriver, wrench (spanner for you lot in the UK), or worse.
Actually, before I was writing blog posts on fleet management software I was doing boat maintenance. One thing you can’t afford to do on a boat is losing tools because it’s hard to find a Sears in the middle of the ocean. Having the right tool for the job becomes a necessity, not a luxury.
So, when you go over the side for a quick repair, you make sure to tie your tools to your toolbelt with strings and ropes. You bring only the minimum required tools for the job, even if it can cause an inconvenience. And you work with extreme care.
As a field tech, you know that looking professional is all about having the right tools for the job. Consider that your job was not to lose your tools. Then, you’d need to have the right tools for that job. This may sound weird but if your job is not to lose tools then you need the right tools to help you not lose your tools. Think of the guide below as a virtual toolbelt filled with the best tools designed to make sure you, well, don’t lose them.
Nothing beats an organized toolbox
The thing with toolboxes is this, they all start out organized until we put the tools in. No one wants a disorganized toolbox but you usually get a disorganized toolbox like this:
- Start out with a set of tools that you have or plan to buy.
- You then buy a toolbox to house the tools you need/have.
- As time goes by, you accumulate more tools and the toolbox becomes too small and overcrowded.
- A messy toolbox shortly follows.
- You start losing tools.
- The other option is that you’ve lost so many that your toolbox is now too big and you have trouble finding tools.
What’s the solution? As Goldilocks will be very happy to tell you, you need a toolbox that is just right. That means – don’t be stingy. If your toolbox is too big or too small it’s time for a new one. You’ll pay it back in tools not getting lost.
Hang it on a string
Now that you have the right tool(box) for the job it’s time to add some improvements and make your toolbox your own. Working on a moving platform, like a boat, means that everything needs to be tied down, fastened, and secured. No doubt, this can be an uncomfortable working environment.
On the other hand, it’s a great way to develop some skills that help you stay organized. For example, when working on a boat, you can’t just leave your drill on the floor because a wave could knock it over straight into the water and bye-bye Black & Decker.
My advice to you is to put it on a string or in a bucket. Even if you don’t have to work on a boat, and don’t need to worry about your drill ending in the bottom of the ocean, you should start putting your stuff on a string.
Yes, at first it will be annoying and it will create an additional headache you haven’t had to deal with until now. But, if you’re reading this article you’ve probably lost a tool or three and you do get used to it after a while. Just ask window cleaners:
Tip: for some tools it’s best to use a stretchy string also known as a bungee cord. It’s advantageous because you can still maneuver your tools easily, and you need less string, which means it’s also tidier.
Organized tool boxes mean happy techs
This one may seem pretty obvious. At some point, we’ve all let our toolbox organization go because we were too busy, too tired or lent it to someone else and he made a mess of things and we were too tired to put everything back in place.
If you want a clean and organized toolbox I have a suggestion for you, and you may not like it. At the end of every day, clean out your toolbox completely. Put everything back into storage (in the van or at the office). Tomorrow, you’ll put in your toolbox ONLY the tools you need for that particular day and then, again, empty it out at the end of the day.
Tip: Some of you may not have anywhere to keep tools other than your toolbox. For you I suggest having two toolboxes. A large one where all your tools live, and a small one (can also be a tool belt) for daily jobs. This is a great way to prevent yourself from losing tools and saving you a lot of time while on the job.
Habits and routines
I don’t want to dance around the topic too much so let’s talk about your work habits and routines. The real key to keeping track of your tools and not losing them is developing habits and routines. There are several routines you can develop to prevent losing tools while on the job. These are the ones that have worked for me:
A. End-of-day checklist
The best way to get into a productive routine is to force yourself into one. Create a checklist to close out your day. You can add stuff like:
- Did you start collecting your tools 15 minutes before EOD (so there’s no rush)?
- Did you walk through the job site and make sure no tools have been left behind?
- Did you place tools in their proper place?
- Did you take your toolbox with you?
- Is anything missing?
- If yes, write down what it is (it’s important to note what went missing where and when. I’ll get back to why that’s important later)
I’m sure you can add more as you go along. By the way, there’s an app for that:
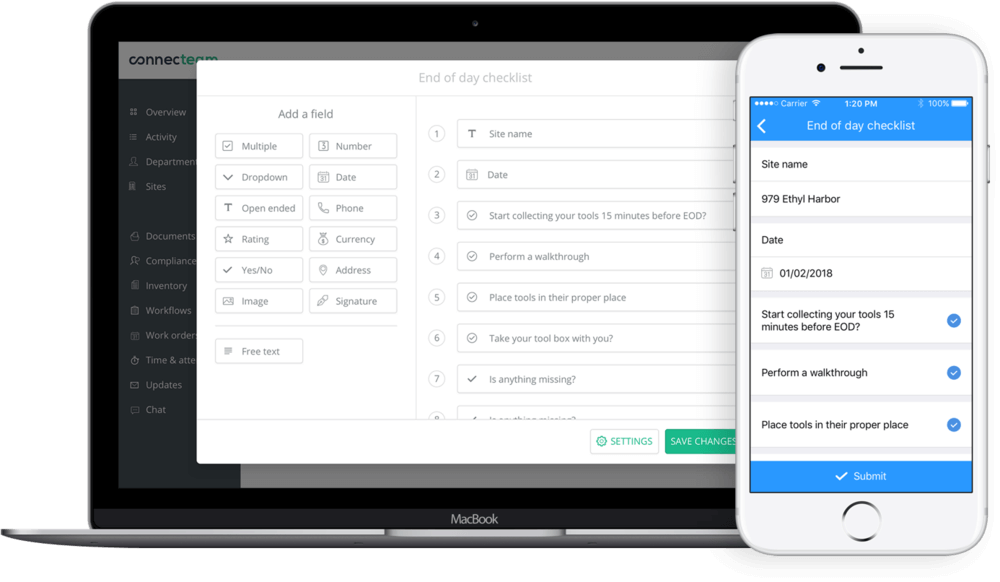
Make all checklists & forms digital
Whatever your habits and routines, Connecteam makes it easy to directly access all checklists and forms from any location. In a tap, employees can fill out the end-of-day checklist, equipment sign out form and more.
B. Create an equipment sign out form
An equipment sign out the form is different from an inventory listing. An inventory listing lets you know what tools you have at your disposal. I’m pretty confident that most of you do inventory once in a while, depending on the size of your business and other factors, and that’s fine. An equipment sign out the form is a daily log of the tools being used by each tech. Every tool that leaves inventory and goes out on the field needs to be signed out using the equipment sign out form and signed back in at the end of the day.
The equipment log is a huge help in keeping your tools safe and sound. However, it can be very time-consuming. Especially, if it requires your field techs to come back to and leave from the office every day. That’s extra gas mileage and time on the clock that could make the whole process of logging equipment simply not worth the hassle.
Instead, you can ask your tech to fill equipment logs from a mobile app. That way, you can still keep track of your tools at all times and save that gas money. Here’s an example of what that would look like:
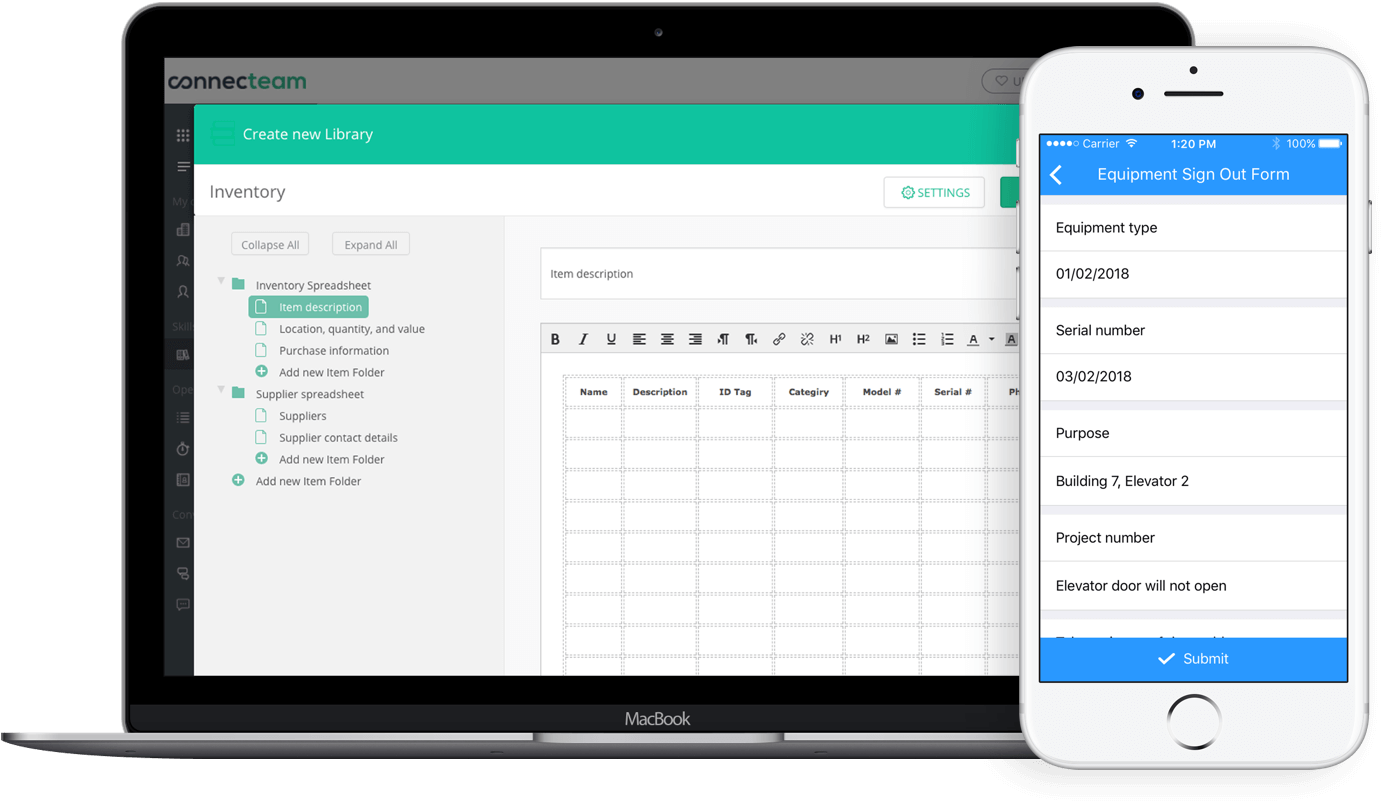
When you create an equipment log using the Connecteam mobile app, it is also saved in the manager’s LaunchPad. From there, a manager can have access to all daily logs, filter through them, and find the one they need anytime.
c. A single place (where tools live after a shift and are always returned there)
I addressed this before but it’s worth repeating. Your tools need a home. Just like you start your day from home and return to it your tools need that same type of security or they get lost. I know it can be a pain in you know what but it’s totally worth it. Routines and organization are what separate the professionals from the DIYers. Once you start working this way you’ll also feel better about yourself and your professional conduct.
If you like it: put a sticker on it
For your more pricey ticket items place stickers with information on how to return to the owner. Maybe even offer a reward.
Keep a drill bit and screw tub
for the smaller stuff, it may be annoying to sort through nails, screws, and drill bits. So bring a tub to your van or truck and throw all the small stuff in. Then once a week, take an hour to organize everything back to the office inventory.
Create a daily job listing
with tools to be used and go along the list daily. That way, if you lose something you can trace your way back to when and where you lost it. Good chance it’s still on a floor somewhere just you didn’t know where to look.
Focus on what you lose the most
As they say, the best offense is a good defense. Figure out what stuff you tend to lose the most and focus on making sure you take care of that stuff. For example, if you tend to lose drill bits, it might be worth investing in a new case or developing a work process where you put away a drill bit right after using it, even if you mean to use it again later.
Your time is money, for you and your employer. If you spend your entire day looking for lost tools, good chance you’re going to get the crook eye from your boss or worse. So to sum up, prevention is key here. Being organized and developing work processes to prevent losing tools can save you a lot of time and money and improve your productivity.
Don’t lose tools on the job site with Connecteam
Employees can fill equipment logs from Connecteam’s mobile app. That way, you can keep track of your tools at all times and save that gas money. When you create an equipment log using Connecteam, it’s also saved in the manager’s Launch Pad. From there, a manager can have access to all daily logs, filter through them, and find the one they need anytime.